So Far, So Good: Pandemic Tests Resilience of Data Center Supply Chain
We conclude our Data Center Executive Roundtable today with a look at the data center supply chain and how it is faring with the global business lockdowns during the COVID-19 pandemic. We explore this topic with our panel of data center executives, including John Sasser of Sabey Data Centers, Phillip Marangella of EdgeConneX, CoreSite’s Steve Smith, Scott Walker from NTT Global Data Centers Americas, and Nancy Novak from Compass Datacenters and Infrastructure Masons.
The conversation is moderated by Rich Miller, the founder and editor of Data Center Frontier.
SCOTT WALKER, NTT Global Data Centers, Americas
Scott Walker: The good news for data centers is that most – if not all – of our supply chain has been classified as essential businesses. As a result, the supply chain has been minimally affected for us as we continue construction at our data center campus sites in Chicago, Hillsboro (Portland), Silicon Valley, and Ashburn.
Early in the pandemic, there was some concern (and there still is to a limited degree) that second- and third-tier vendors would not be able to provide components. But for the most part, that concern has been mitigated.
We are, however, staying close to our providers to monitor any changes. The biggest challenges we face are the social distancing restrictions put in place by each region’s local Authority Having Jurisdiction (AHJ). These restrictions are forcing our contractors to look at staffing in a different way, and could possibly lead to increased costs going forward. Despite these challenges, we are on track to bring new capacity online later this year at affordable price points for customers of all sizes.
NANCY NOVAK, Compass Datacenters and iMasons
Nancy Novak: Maintaining a level of development and construction to keep supply level with demand is only going to be an increasing challenge. Right now, being able to deliver a facility in six months is becoming more of a standard requirement, and I’m not sure how much more time can be shaved from that timeframe.
The new challenge will be to be to maintain that level of velocity across multiple locations here in the U.S. and internationally. In order to compete in this new landscape, it is going to require providers to tighten their supply chains to ensure that critical components, particularly long lead parts, and materials are available in synch with schedule require of course.
However, the most important areas for providers to ensure that they are successfully leveraging technology (BIMs, VR/AR, etc.) in both the design and construction phases of their efforts. Capabilities like VR, for example, identify potential problems before they are discovered on the job site to help ensure schedule integrity. Technology will also be important in helping to provide the number of personnel required to support multiple projects. Advances in exoskeleton functionality is just one area that enables women to become more active participants on the jobsite, thereby helping to address the needs for an expanded labor pool.
STEVE SMITH, CoreSite
Steve Smith: With an unplanned, global health crisis like the COVID-19 pandemic, supply chains across many industries are affected, including data center infrastructure. If you think about it, all components of a data center are built off-site, delivered, and then installed – there are many opportunities for the supply chain to break. Individual parts of UPSs, CRAH units, among other machines, are sometimes built in different countries or states than where the product will be manufactured. Then getting the unit to and into the data center is a separate process. The number of people, resources and effort to coordinate this process is complex and critical.
In the midst of the pandemic, CoreSite delivered its CH2 data center—the first purpose-built data center in downtown Chicago—on schedule. Thankfully, when the pandemic took effect in March, we were deep in the construction process and didn’t experience a delay. During construction, and due to stay at home orders and social distancing measures, the corporate team wasn’t able to visit the site as often as we typically do. We completed inspections and commissioning virtually, and worked closely with our general contractor to ensure proper installation of equipment.
We are expanding in Los Angeles with LA3 and the Bay Area with SV9 and don’t anticipate supply chain delays at this time. We standardized critical construction and data center products, ensuring speed to delivering to capacity to market. Additionally, we’re able to move these assets, if needed, to accommodate a need elsewhere in our portfolio.
PHILLIP MARANGELLA, EdgeConneX
Phillip Marangella: If there’s one thing COVID-19 has tested, it’s been supply chains and data center management processes. Here, diversity in procurement coupled with flexibility and agility in deployment capabilities is the solution to overcoming challenges.
Part of our strength as a company is the speed at which we can build our data center facilities. On average it is between 6-9 months. That is done, in part, by warehousing key equipment so that we can quickly deploy gear where it is needed globally. We also use multiple vendors and source from diverse locations so that we are not single-threaded. As such, we have not experienced any impediments in our build times during the pandemic.
We continue to communicate and collaborate with our vendors to ensure that all of our current expansions and planned builds will be ready for service per our commitment to our customers.
JOHN SASSER, Sabey Data Centers
John Sasser: Management and stewardship of power is a signature strength for Sabey and we are continually looking for ways to increase efficiency.
As far as other requirements, we have seen some increased lead times, but for the most part, our projects have not been greatly affected by supply chain issues. Still, we will be focusing on ways that we can bring these more in our control, including maintaining a larger inventory of materials on hand than has been our custom and adopting optimizing procurement practices.
RECAP: Links to all the Roundtable articles and Executive Insights transcripts for all our participants.
Keep pace with the fact-moving world of data centers and cloud computing by following us on Twitter and Facebook, connecting with me on LinkedIn, and signing up for our weekly newspaper using the form below:
About the Author
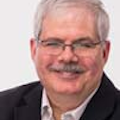