Comparing and Contrasting Liquid Cooling Technologies
The global adoption of AI is traveling with unfriendly companions; extreme energy consumption and the heat byproduct servers produce while keeping up with expanding demand. Liquid Cooling is one technology seeking to turn down the heat.
Liquid Cooling improves the energy efficiency of data centers, saves valuable space, reduces water usage and dramatically cuts energy costs.
Two prominent cooling techniques are Single Phase Immersion Cooling and Direct-to-Chip Cooling. Here's a detailed bullet-point chart to compare and contrast these two methods:
Single Phase Immersion Cooling
Description:
- In Single Phase Immersion Cooling, electronic components are fully submerged in a non-conductive dielectric fluid. The fluid absorbs heat from the components, and since it is single-phase, it remains in liquid form throughout the process.
Advantages:
- Uniform Cooling: The entire component is uniformly cooled, as the dielectric fluid directly surrounds and touches the components.
- High Heat Dissipation: The method can handle high heat loads, as the liquid has a high heat capacity and can efficiently transfer heat away from components.
- Reduced Cooling Infrastructure: Since the system does not rely on air circulation, it eliminates the need for fans, air conditioning units, and large cooling infrastructure.
- Noise Reduction: With the removal of fans and other air-moving components, noise levels are significantly reduced.
- Environmental Control: Immersion cooling systems are relatively isolated from environmental factors, such as humidity and dust, which can be beneficial in harsh environments.
Disadvantages:
- Fluid Management: The choice and management of the dielectric fluid are crucial. It can be expensive, and its long-term stability and compatibility with materials must be ensured.
- Maintenance and Accessibility: Maintenance can be challenging, as components need to be removed from the fluid for servicing or replacement.
- Initial Setup Cost: The infrastructure for immersion cooling can be costly, especially for retrofitting existing data centers.
Direct-to-Chip Cooling
Description:
- Direct-to-Chip Cooling involves using cold plates or heat sinks attached directly to the chips or processors. Coolant (usually water or a refrigerant) is circulated through these cold plates, removing heat directly from the chip surfaces.
Advantages:
- Efficient Heat Transfer: Direct contact with the chip surfaces allows for efficient heat transfer, effectively cooling high-power components.
- Component Accessibility: Components are more accessible for maintenance and replacement compared to immersion cooling.
- Scalability: The system can be easily scaled and integrated into existing data center infrastructures.
- Lower Fluid Volume: Uses less coolant compared to immersion cooling, which can reduce fluid management complexity.
Disadvantages:
- Limited Cooling Surface: Only the areas in direct contact with the cold plates receive cooling, which can lead to hot spots if not properly designed.
- Complex Plumbing: The system requires a complex network of tubing and pumps to circulate the coolant, increasing the risk of leaks and mechanical failures.
- Noise: Pumps and fans used in the system can generate noise.
- Dependence on Air Cooling: Often, direct-to-chip cooling systems are used in conjunction with traditional air cooling for non-liquid-cooled components, meaning that some air cooling infrastructure is still necessary.
Comparison and Contrast
- Cooling Efficiency:
- Immersion Cooling provides uniform cooling and is highly effective for high-density computing environments.
- Direct-to-Chip Cooling offers targeted cooling for specific high-power components but may not cool the entire system as uniformly.
- Maintenance:
- Immersion Cooling requires special handling for fluid and can complicate maintenance and upgrades.
- Direct-to-Chip Cooling allows easier access to individual components for maintenance.
- Infrastructure and Cost:
- Immersion Cooling has a higher initial setup cost and may require specialized facilities.
- Direct-to-Chip Cooling can be more easily integrated into existing systems, potentially lowering costs.
- Environmental and Operational Factors:
- Immersion Cooling provides excellent environmental isolation and is quieter.
- Direct-to-Chip Cooling may require additional air cooling infrastructure, leading to higher noise levels and sensitivity to environmental factors.
- Fluid Management:
- Immersion Cooling involves handling large volumes of dielectric fluid, which can be costly and requires careful management.
- Direct-to-Chip Cooling uses smaller volumes of coolant, typically water or refrigerant, which may be easier to manage but introduces the risk of leaks.
Liquid cooling in the data center doesn’t have one distinct winner; the choice between Single Phase Immersion Cooling and Direct-to-Chip Cooling depends on various factors, including the specific requirements of the data center, budget constraints, and the desired level of cooling efficiency and infrastructure complexity. Choosing the right fit for the application and project is critical for short-term results and long-term strategy.
About the Author
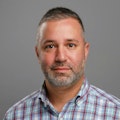
Chris Carreiro
Chris Carreiro is Chief Technology Officer at Park Place Technologies. Park Place Technologies provides solution and vendor-agnostic, turnkey liquid cooling solutions to companies across the globe. Click here to watch our latest webinar.