Fuel Resiliency Demands More Than Just a Fuel Supplier
In the high-stakes world of data centers, where even second of downtime can trigger cascading consequences, backup power systems are rightfully treated as essential. Yet while most facilities invest heavily in redundant generators and switchgear, far fewer examine the weak link that often undermines it all: fuel delivery logistics.
Fuel resiliency isn’t simply about having a full tank before the storm hits. It is about understanding the infrastructure needed to keep those tanks full during an extended outage—especially when the rest of the region is in crisis too.
The Myth of the Metered Pump Truck
During routine data center operations, fuel is typically delivered via metered pump truck—4,000-gallon vehicles with flow rates ranging from 60 to 100 gallons per minute. These are well-suited to topping off tanks one by one during planned downtime. But in an emergency scenario where multiple generators are running simultaneously, these trucks become bottlenecks.
Let us consider a hypothetical data center campus with more than 60 generators spread across two enclosed yards. Under load, the generators could collectively consume over 7,000 gallons of fuel per hour. A metered pump truck, constrained by access, hose length, and flow rate, might offload only 2,000 gallons per hour. It would take at least four trucks working continuously to meet demand. But given delivery time, return logistics, and driver hours-of-service regulations, sustaining that rate might require 18 to 24 dedicated pump trucks in rotation.
These trucks account for only a small percentage of available fuel delivery assets in most regions. In a widespread outage, data center operators will be competing for a limited pool of specialized equipment—fighting over the same limited resources..
Planning for the Realities on the Ground
Access is another frequently underestimated constraint. Generator yards are fenced and secure, often with just one or two gated entrances. This layout is required for physical security, but extremely detrimental to fuel delivery logistics. Trucks with standard hose lengths may find themselves more than 150 feet from the nearest fill point. That means longer hoses, added manpower, slower turnaround, and increased risk of spills.
At many campuses, the layout varies by building, and so do the access points. Even if a truck is capable of reaching the equipment, the tight roadways and individual generator orientations compound the complexity of delivery.
Assuming you could get enough trucks—can they even reach the tanks in time?
Rethinking Delivery Assumptions
In contrast to metered pump trucks, larger 7,500-gallon transport tankers represent the majority of the available fuel logistics fleet. These transports do not pump fuel to individual tanks, but with the right infrastructure, they can offload fuel in 35 minutes—less than half the time required for a pump truck to manually “wet hose” just a few generators.
But most data centers are not designed to receive fuel this way. There is often no centralized offloading point or bulk storage tank. There is no high-flow connection, no automated distribution system, and no scalable method to support continuous refueling at a site-wide level.
That is not a supplier problem—it is a planning problem.
Resiliency Is an Engineering Exercise
As the industry pushed toward operational excellence and sustainability, resiliency must be engineered, not assumed. That means:
- Modeling fuel consumption based on real-world load expectations.
- Evaluating how many trucks, what type, and with what frequency are needed in an outage.
- Testing whether access points and delivery paths support continuous fueling.
- Planning for weather, road closures, and market disruptions—not just equipment failure.
It is tempting to focus only on capacity (how much fuel can be stored), but resiliency is also measured in flow—how consistently and rapidly that fuel can move where it is needed, when it is needed.
A Real-World Lesson in Fuel Resiliency
In a recent event, a major data center campus experienced an unplanned, extended, generator run when a localized power outage forced it onto emergency generator power. While the site had fuel supply contracts in place, the reality on the ground exposed critical weaknesses across every element of fuel resiliency.
Firstly, the ramp up time to initial delivery from the emergency supply contracts took significantly longer than expected. Initially topped off, tanks soon dropped to 50% or less in many cases. This forced an urgent rush to replenish expended fuel reserves, not just maintain levels.
Secondly, design limitations played a central role. The facility relied on individually filling all generator tanks, with many being incapable of accepting high-flow deliveries from available deliver equipment. This design forced inefficient workarounds, such as truck-to-truck transfers on-site, adding unnecessary steps and delays. Additionally, inadequate hose lengths and restricted access routes limited reach and flexibility.
Thirdly, there was a clear gap in monitoring and communication. There was no central location for monitoring all tank levels. Although tank levels were being regularly checked individually, information only flowed in one direction – to the site – with little to no real-time feedback to the fueling teams on where fuel was urgently needed. As a result, trucks sat idle, full, and awaiting direction, while generators approached undesirable low fuel levels.
Fourthly, the maintenance and operational readiness of the overall system was compromised by rigid adherence to normal operating procedures, instead of transitioning to streamlined emergency protocols that maximize delivery efficiency.
Finally, personnel and training emerged as a critical vulnerability. Emergency preparedness training was insufficient, and there was minimal flexibility or authority to escalate issues and adapt to rapidly changing conditions. Inefficient delivery processes also increased the number of required operations staff on site significantly
Although no load was ever dropped, the consequences were significant: emergency resources were wasted, operational staff were stretched very thin, the risk of mistakes elevated significantly, and the financial cost to mitigate the event was greatly increased.
This real-world event demonstrates that fuel resiliency is not merely about having enough fuel on contract. It requires a holistic approach that integrates robust design with centralized monitoring and fueling, dynamic communication, proactive maintenance planning, appropriate and adaptable compliance measures, and trained personnel ready to implement emergency procedures without delay.
Conclusion: Start the Conversation Now
The best time to plan for fuel resiliency is long before the outage. Facility engineers, operations leaders, and procurement teams need to ask harder questions—not just about price per gallon, but about feasibility, equipment availability, personnel training, emergency preparedness, and the site’s physical limitations.
When the grid goes down, and your generators are the last line of defense, your assumptions will be tested. The question is not “Did we order enough fuel?” It is “Can we keep the tanks generators fueled when resources are limited?”
About the Author
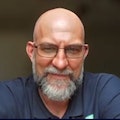
Andrew Holmberg
Andrew Holmberg is Chief Engineer and Director of Innovation at ESI Total Fuel Management, where he leads engineering, product development, and technical strategy for mission-critical fuel systems. This article was developed in collaboration with Brittani Clarke Clayman, Director, Marketing and Communications, ESI Total Fuel Management.
ESI Total Fuel Management serves the global data center community with expertise and leadership, providing innovative fuel solutions that increase generator uptime and ensure environmental compliance in response to fuel-related threats.