Right-Sizing for the Edge: Data Center Design in Secondary Markets
For data center providers, success in second-tier markets requires building in the right place, and at the right size. Matching the size of the data center to the level of demand is one of the oldest challenges for data center developers.
As the action shifts to smaller markets, designs must balance reliability and flexibility. Mistakes can be expensive, as data center construction costs range from $5 million to $15 million per megawatt of capacity.
That’s why modular design and lean construction methods are playing a major role as the data center industry looks to deploy capacity in new places. As data moves to the edge of the network, data centers are being right-sized to fit the demands of these new markets, deploying space in digestible chunks.
For data center providers, decisions about local markets are driven by risk and economics. The 25-megawatt “aircraft carrier” data centers seen in major Internet hubs and cloud campuses are poorly suited to local markets, where the requirements will be considerably smaller.
This is the third in a series of stories at Data Center Frontier on the changing data center geography of the United States. Previous installments have looked at how wired businesses are driving local demand for data center services, and how the data-hungry consumer is influencing where content resides on the Internet. Today we explore how the push into smaller markets is influencing data center design.
After years of focusing on building bigger, the growth of regional markets is supporting a focus on smaller data centers that can be built affordably and expanded in phases. Modular design and pre-fabricated construction are playing a key role in these deployments, but are being applied in a variety of ways.
Real Buildings, 1.2 Megawatts at a Time
One of the long-standing arguments for IT outsourcing is that it doesn’t make economic sense for an enterprise to build a 1 megawatt data center. If that’s true, does it make sense for a data center developer to build a 1 megawatt facility?
Chris Crosby says it does, and has pursued this approach with Compass Datacenters, which specializes in building data centers in untapped growth markets. Crosby founded the company in 2011, seeking to bring the wholesale data center product to cities where demand is growing, but hasn’t yet reached the scale of historic data center strongholds like Silicon Valley or northern Virginia.[clickToTweet tweet=”Modular data center designs are playing a key role, but being applied in a variety of ways.” quote=”Modular data center designs are playing a key role, but being applied in a variety of ways.”]
A key task for Compass was optimizing its data center design to fit the demand profile of smaller markets, while deploying its development capital in an efficient manner. Its solution offered a mix of standardization and flexibility: a 1.2 megawatt data center dedicated to a single customer, but offering a menu of options to address different requirements.
This approach allows Compass to standardize its design, using pre-fabricated components to control cost and speed to market, while acknowledging that no two customers are alike. It describes the design choices as “personalization, not customization.”
“It’s like a spec home,” says Crosby. “We have tons of options for customers to make it their own.”
Matching Economics and Design
That includes expansion, as customers can add capacity in 1.2 megawatt chunks, with Compass constructing additional buildings that are connected to the original facility. Customers have the option of building on their own property, or leasing a site and building from Compass. There’s even a lease/purchase option.
“From a scale perspective, people think it can’t work,” said Crosby. “It defeats all the economic principles of scale. Most service provider business models work at scale only – meaning putting a megawatt in Des Moines doesn’t make economic sense. But if you don’t use (the larger footprint) you don’t need the benefits of that approach. We’re not a big gigantic colo facility.”
Cost control is crucial. Crosby no longer uses the term “modular” to describe the Compass approach to data center design and construction, saying the term is confusing to customers. But Compass embraces lean construction techniques and pre-fabrication to gain consistency on cost and delivery schedules.
Compass data halls are at least 10,000 square feet, and are designed without columns, providing more room for customer IT equipment. (Photo: Compass Datacenters)
“It’s real buildings, and concrete and steel,” said Crosby. “Components like our PowerCenters (electrical rooms) are built off-site and shipped to the location for installation. The walls of our facilities are pre-fabricated, structural pre-cast and then erected on site. It’s all about these types of efficiencies. So if we are defining pre-fabricated from this perspective, I would say that it’s making very positive impact on the industry and will continue to become more pervasive in the future.”
These lean processes give Compass the ability to build in as many as six markets at once, according to Crosby.
“I’m more convinced than ever about this being the right approach,” he said. “The market wants this type of product. That ability to go anywhere has proven very, very valuable.”
The Road to the Anywhere Data Center
IO believes the data center should be available anywhere – large markets, small markets, on premises, in one of its data centers or even outdoors.
It was the first multi-tenant data center provider to offer modular designs, and sees the modular form factor as an important key to its success – including its ability to quickly deploy space in second-tier markets like Dayton, Ohio.
“When we roll into a new market, we’re able to take advantage of our platform from day one,” said David Mettler, VP of Sales and US market director for IO. “Other providers may have to retrofit an existing facility. Our model allows us to enter the market in a way that’s efficient. We can deploy what we need, when we need it.”
In Ohio, that means a 40,000 square foot facility with 5 megawatts of power – a stark contrast to the massive data centers IO has built in Phoenix and New Jersey, which each offer more than a half million square feet of space.
Rows of BASELAYER Anywhere modules inside the IO Ohio data center near Dayton, Ohio. (Photo: IO)
IO deploys its capacity in modules built by BASELAYER, which was spun off by last year and sells the modular data centers and data center management software developed at IO. Each module offers 400kW to 1.5 megawatts of capacity, including raised floor space configured to house between 18 and 50 cabinets of IT equipment. The modules are offered in Core or Edge configurations, as well as an Eco model that uses fresh-air cooling.
The modules are manufactured in a BASELAYER factory near Phoenix, and then shipped to Ohio, where they are installed inside the IO Ohio facility, which is adjacent to a major highway.
“It’s very attractive to us to say we use a standardized data center deployment,” said Mettler. “As a service provider, we have a very robust understanding of the operating environment. We have been gaining so much information about how our platform works. Every day we can assess our operations and make decisions about the best way to operate our data centers. When our customers see that, they’re pretty impressed.”[clickToTweet tweet=”IO’s David Mettler on modular design: We can deploy what we need, when we need it.” quote=”IO’s David Mettler on modular design: We can deploy what we need, when we need it.”]
When a customer needs additional data center capacity, they can purchase an additional module, adding new space in increments as small as 400kW at a time.
“We help make the future less risky for our customers because they can grow with us,” said Mettler. “Our modules operate extremely efficiently. The economic advantages of this become really pronounced at the wholesale level. They save money with our model.”
Mettler says IO Ohio offers a model for how modular designs can work well for both customers and service providers.
“We see it as a nice example of our ability to deploy capacity in new markets,” he said. “We’re excited about how the Dayton model has worked.”
Schneider Electric Sees Micro Opportunity
Providers aren’t the only ones who’ve seen the potential for modular designs in second-tier data center markets. Schneider Electric has been steadily boosting its capabilities in modular design, both with its in-house product lines and the acquisition of AST Modular in early 2014.
Schneider worked closely with Ubiquity Mission Critical Solutions on a concept to create a national chain by converting Sears Auto Centers in second-tier markets into data centers. The plan called for Schneider to deploy mechanical and electrical equipment on prefabricated modular skids that would each support 600kW of capacity. Cooling would be provided by Schneider EcoBreeze units, which can automatically switch between several cooling modes based upon local weather conditions, using free cooling on cool days and an on-board refrigerant cooling system on warmer days. This versatility allows EcoBreeze to be deployed in different parts of the country.
Schneider Electric’s suite of modular data center products. (Image: Schneider Electric)
Ubiquity, a unit of Sears Holdings, ultimately opted not to pursue the project. But Schneider has continued to work with service providers to target opportunities to apply modular designs and repeatable construction processes in secondary markets.
One example is DartPoints, which is seeking to build a national “private colo” network of micro data centers, offering managed colocation space in small, distributed modules. DartPoints worked with Schneider Electric to develop preconfigured 100kW data center modules that include a UPS unit, in-row chilled water cooling units, and hot aisle containment systems. Using 100kW increments provides DartPoints with the flexibility to cater to a customer’s geographic needs and the adaptability to grow as they go.
Schneider sees micro data centers as the key for unlocking an even bigger opportunity going forward: The Internet of Things.
“The use case on the horizon with the greatest potential is a massive distributed network of micro data enters to form a content distribution network,” writes Steven Carlini, Senior Director of Data Center Global Solutions for Schneider Electric. “This processing on the edge will support the commercial Internet of Things (IoT), including the fast emerging category of wearable devices. The processing of data could be reduced to milliseconds here.”
A recent research report projects that micro data centers will proliferate at the “edge” of the network, driven by content distribution and the Internet of Things, with a potential value of $6.3 billion by 2020.
And Then There’s the Central Office …
In the meantime, Schneider also sees retrofit opportunities in smaller markets, especially thought the conversion of former central offices for telco providers.
“Tilt your head a little, and you’ll see central offices are already a lot like data centers,” writes Mark Hurley, an executive manager at Schneider. “They’re mission critical facilities with mission critical infrastructures, prime for adaptation to a new economy of digital capacity and availability. Being close to the user with the foundation in place to support the demand for more connectivity, capacity and speed translates into a tremendous business opportunity.”
Chris Alberding would certainly agree. Alberding is the Vice President of Product Management at FairPoint Communications, a New England telco that has been converting its old central offices into data center space.
“We’re not building out the 20,000 or 30,000 square foot data centers,” said Alberding. “We’re building what we call micro datacenters.”
FairPoint has done two retrofits of central office space in New Hampshire, a 6,000 square foot site in Laconia and a 4,00 square foot facility in Manchester. The company expects to bring another 4,000 square feet online next March, and has a handful of surplus central offices it can convert for future expansion.
“Going forward, we look at 4,000 square feet as the minimum,” said Alberding, who said their design can accommodate 130 to 150 racks, and offers about a 3.5 year payback on investment. “Northern New England is not a massive growth market, but there’s definitely a need there.”
About the Author
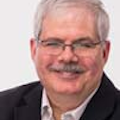