Building Data Centers for Operational Excellence: Disaster Prevention Starts Long Before Shovels Hit the Ground
Data centers are growing in size and complexity in the race to meet the needs of our digital economy and AI. Yet no matter how much data centers are changing, the owner’s goal for each new development remains the same: build a critical facility provisioned with the right people and processes to run uninterrupted for the next couple of decades.
That’s a tall order, especially at a time when finding qualified staff experienced in operating critical facilities is becoming harder each day. In my many years working in the industry, I have seen one stage in the development process that holds the greatest potential for things to go awry — the transition from construction to ongoing operations. That transition is rarely as smooth as owners would like it to be, but there are ways to mitigate these risks.
The secret to a successful transition is to engage facilities management (FM) and operations and maintenance (O&M) stakeholders long before the first day of operations. They should be active participants during the programming, design, construction, testing, and of course transition to operations. The following are five steps to create a smoother transition from construction to long-term operations.
1) Establish O&M requirements during programming
Development of a new data center starts with creating the owner's project requirements (OPR) document, which informs the architects and engineers of the project’s goals. The OPR defines basic requirements, such as the data center’s size and the potential disasters it must be able to survive.
At that time, you also need FM/O&M stakeholders in the room to help decide how the building will be operated and maintained over the long haul. This is the time to plan how the FM department will be organized, which processes to employ, and whether various activities will be performed in-house or outsourced. All these decisions will impact the facility’s design and related project deliverables.
2) Embed FM/O&M in the design
Once the O&M requirements have been established, the engineer-of-record must address them in the basis-of-design and construction documents. For example, if you plan to handle maintenance in-house, you may need a machine shop, an electric shop, and places to store spare parts and tools.
The facility’s design should also address unique data center O&M requirements, such as including sufficient space to access equipment and ample emergency lighting in areas where crews may work to reestablish power after an outage.
At this point in the process, it is also helpful to specify O&M conventions and project deliverables, such as equipment naming conventions and standard operating procedures, to ensure they are consistent and informative for the staff who will run the facility.
3) Set the stage for efficient operations during design
While the engineers and architects prepare design documents, the O&M and FM teams can lay the groundwork for efficient operations. They can create a training plan and specify the documentation needed for ongoing operations, including the Systems Operations and Maintenance Manuals (SOMMs). Thoughtfully planning the format, organization and content of manuals will ease the way for staff over the long term.
Additionally, the O&M team should define what ongoing support they will require from equipment vendors. Negotiating service-level agreements before purchasing equipment gives you the most leverage and secures the deepest discounts.
4) Embed O&M in the construction phase
I encourage teams to embed FM and O&M deliverables and training milestones in the general contractor’s master construction schedule to help keep them on track.
It’s ideal to establish a “closeout” documentation repository and SOMM organization at the beginning of construction. Then, you can drop in all record documents as they become available and build up your systems operations and maintenance manuals.
This is also the time to populate the computerized maintenance management system (CMMS) with the building and equipment details and to begin training staff, so they are ready to go live.
5) Embed O&M staff and requirements in the commissioning process
In the final stage of development, the commissioning team (including representation from FM/O&M) will validate that the goals and objectives in the OPR, as specified in the construction documents, have been satisfied.
Ideally, the O&M staff should be active participants in commissioning. The acceptance testing of the built facility can be the best O&M training they ever receive. The commissioning philosophy is to identify and resolve issues and discrepancies as early as possible to minimize impacts on schedule, quality, and budget.
Operational excellence begins before go-live
Running a 7x24xForever critical facility requires discipline, training, process-driven procedures, and a culture of excellence. The best way to avert disasters is to embed these elements throughout the design and construction process.
When you consider operational needs along every step, from programming and design to construction and commissioning, it’s possible to build a facility and provision the FM/O&M staff optimized on “Day-1” for disaster prevention and create a smooth transition to ongoing operations.
About the Author
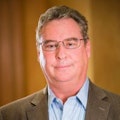
Terry Rodgers
Terry Rodgers is Vice President of Commissioning and Building Analytics at JLL and has over 40 years of progressive experience in critical facilities operations and management including strategic planning, critical infrastructure design, operations, and commissioning; business protection and recovery; preventive and predictive maintenance; and technical training development. Terry is an ASHRAE Distinguished Lecturer and member of ASHRAE committees TC9.9, SSPC 90.4, SSPC-127, SSPC-300, GPC-0.2 and GPC-1.6P.
JLL has a team of 40 dedicated commissioning professionals across North America that specialize in critical environments. Utilizing in-house purpose-built tools, JLL proactively manages the project handover process to ensure the facility is positioned for successful long-term operations.